Production system of TOYO ORIMONO
Instead of owning factories, we engage in the development and
manufacturing of textiles through fabless production overseas.
Regarding our main product of woven fabric, by not only concentrating
on weaving process but also paying attention to production techniques and quality control of dyeing,
yarn texturizing, we are able to develop and mass produce highly functional and high quality textiles.
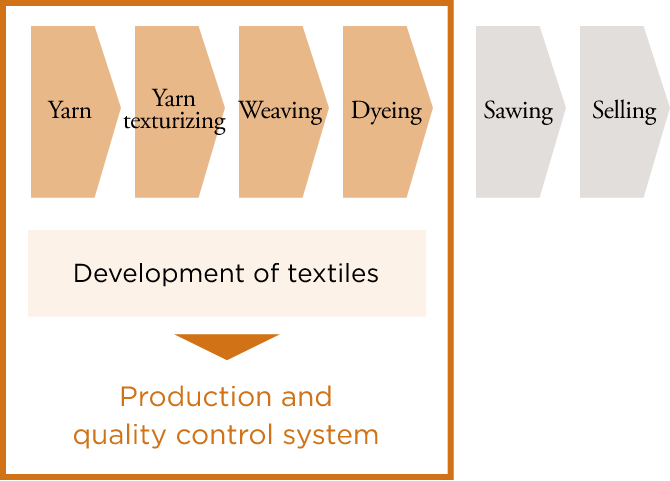
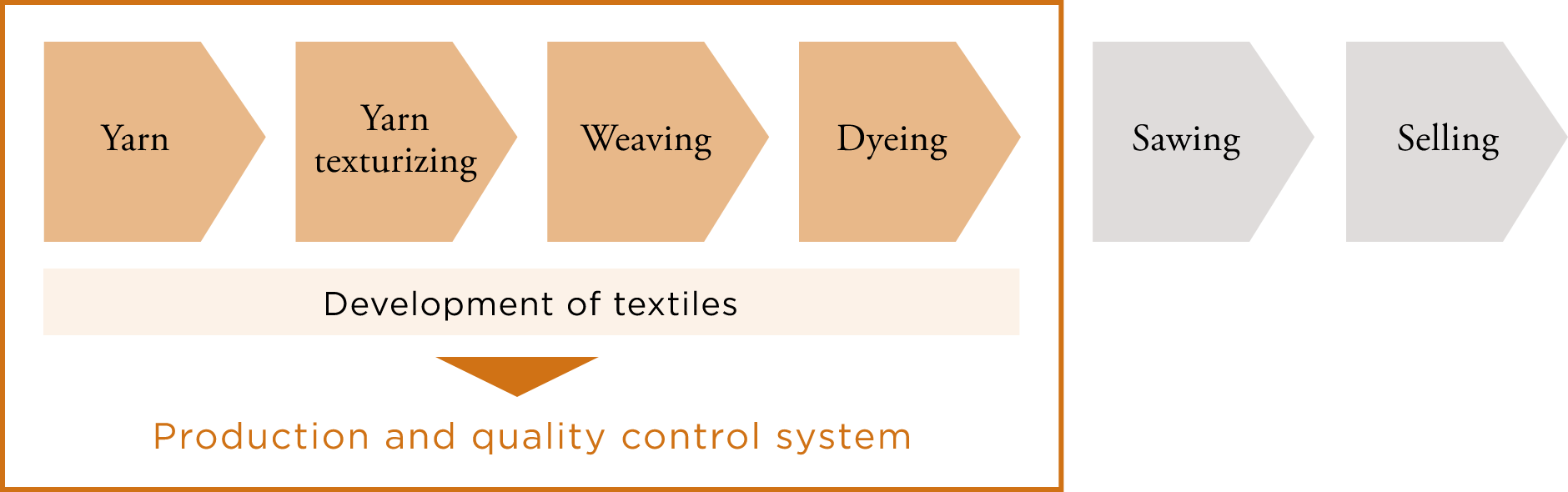
Our production bases
Our production bases are located mainly in Vietnam, but also in Japan, China, and Indonesia.
We use different equipment and material backgrounds in each country according to customer demand.
In our main center of production, Vietnam, Japanese engineers and management staff are stationed long-term at each facility.
We ensure stable supply of our products through quality control, production management, and product development.
Japan
- Weaving
- WJL・AJL
(flat, dobby, jacquard)
- Dyeing
- Dyeing at domestic dyeing plants, various functional treatments
China
- Yarn Texturizing
- Twister machine, false-twisting texturizer, Air texturizer
- Weaving
- WJL, AJL
(flat, cam, dobby)
- Dyeing
- Jet dyeing machine, printer (Transfer, Digital)
- Sewing
- Sewing of ready-made curtains
Indonesia
- Yarn
- Cotton-spinning, Twister machine, False- twist texturizing machine
- Weaving
- WJL・AJL
(flat, cam, dobby)
- Dyeing
- Jet dyeing machine, Printer (flat screen, rotary)
Vietnam
5 Japanese technicians (yarn, weaving, dyeing) stationed,
30 Japanese-speaking Vietnamese staff.
- Yarn
- POY polymerization
- Yarn processing
- Twister machine, False-twisting texturizer, Air texturizer machine
- Weaving
- WJL, AJL (flat, cam, dobby)
- Knitting
- Loop knitting, Warp knitting
- Dyeing
- Polyester dyeing equipment (Jet dyeing machine, heat-setter, etc.),Calendaring machine, Coating machine (dry type), Sanding machine, Transfer printer, Flammability testing machine
- Sewing
- Sewing of ready-made curtains
About our production system in Vietnam
In Vietnam, our Japanese technicians and local Vietnamese staff work together to oversee production and quality control.
Prototyping and mass production process at our Vietnam base:
- 1Strict quality control by Japanese technicians in yarn, weaving and dyeing
- 2Smooth communication with contractor factories by Vietnamese staff who can speak Japanese
- 3Quick response through online meetings between Japan and Vietnam These factors help us achieving speedy delivery while satisfying Japanese strict standards
which is difficult to do only in a local factory in Vietnam.
Quality and delivery management, and visualization of production status
in accordance with Japanese standards.
Introduction of Japanese engineers
and Vietnamese employees
Joined the company in 2007
In charge of yarn texturizing and weaving
Nationality: Japanese
I have been stationed at the current factory since 2007, and it has been 15 years since then. From the time of my arrival to the present, Vietnam has achieved rapid economic development. I feel that our 30 Vietnamese staff members are growing day by day, just like the Vietnamese economy. They are diligent and good with their hands. Making full use of the fact that we present on-site with them, we can conduct thorough quality control with an emphasis on the three ""real"": real place, real things, real time.
In my opinion, the key to quality control overseas is how to get the local leaders and workers of the factories to understand and implement this excessiveness. For this reason, I try to communicate with them not only at work but also in more informal times, such as over meals, so that they can understand how we (Japanese) think and work.
Joined the company in 2013
In charge of dyeing and functional treatment
Nationality: Japanese
Mainly by investigating the causes of manufacturing rework and losses and coming up with countermeasures, we are trying to reduce the defective rate that occurs in dyeing, reduce losses, and meet delivery deadlines. In order to bring the quality level of the products produced at the outsourced factories up to the Japanese level, cooperation from the factories is essential. To this end, we disclose as much information as possible, and in meetings with the factories, we always take their opinions into consideration (and show them that we do), so that we could gain their trust and confidence.
For secondary manufacturing at contract factories, we send special dyeing chemicals from Japan or order them from Japanese manufacturers in Vietnam for trial production, development, and mass production. Since many of the chemicals ordered are expensive, we also manage the actual products.
At TOYO since 2008
In charge of dyeing and processing
Nationality: Japanese
At TOYO since 2000
In charge of weaving
Nationality: Japanese
Our partner factory encompasses the entire process of textile production from upstream to downstream, ranging from the raw material POY through DTY production, yarn processing, weaving, to finishing. This makes it possible to seamlessly manufacture products.
In this context, the key is how to persuade and motivate our partner (partner factory) to take action. For this, explanations drawing on our company's technical expertise and the theoretical understanding of the on-site situation are crucial.
The trusting relationship of our company and the partner factory is built upon experiencing both successes and failures together. Because of this relationship, our partner factory accommodates even our most detailed requests.
With this in mind, I am committed to product development and strive to introduce new products to the market. I have lived in Vietnam for a long time and am married with children. My children are growing up with both Vietnamese and Japanese customs and values. They study at a Japanese school and also work hard in their Vietnamese and English language classes. On weekends, we enjoy small family BBQs together.
Joined the company in 2013
Japanese level equivalent to JLPT examination N2
In charge of overseas sales
Nationality: Vietnamese
For example, it is important to cooperate with the sewing factories to which the products are shipped. If a problem occurs after the fabric has been shipped, we will try to understand the current status of the problem and deal with it as soon as possible by receiving the actual product from the sewing factory or, in some cases, visiting the sewing factory.
We also work together with shipping companies to manage shipments so that we do not have to stop the sewing line due to late delivery.
I believe that the accumulation of each of these efforts will lead to customers' trust in Toyo's products.
In 2019, we established a local subsidiary in Vietnam to sell curtains and clothing fabrics to local Vietnamese customers.
There are differences in the way products are used in Vietnam and Japan, and we are facing some difficulties, but we are expanding our sales with the help of local partners. In the future, we would like to expand this business to countries other than Vietnam.
Joined the company in 2013
Japanese level equivalent to JLPT examination N2
In charge of Dyeing
Nationality: Vietnamese
I am in charge of product quality control and overall quality control at the dyeing factory in Dong Nai Province, Vietnam.
Since there are differences in how people work and think between Japan and Vietnam, I have realized that it is difficult to manage products in Vietnam according to Japanese quality standards.
As a Vietnamese, I have to make sure that fellow leaders and workers at the factories I am in charge of understand and implement Japanese standards for quality control and delivery management.
In order to improve quality, I have to study technical knowledge, quality improvement methods, and management techniques.
I believe it is important to study and improve my abilities in order to improve quality.
Joined the company in 2014
Japanese level equivalent to JLPT examination N2
In charge of weaving
Nationality: Vietnamese
My role in production management includes placing orders to the partner factories based on orders from Japan, organizing yarns needed for production from third parties, and shipping them to the dyeing factories. To avoid delays in delivery, we communicate the delivery date requests from Japan to the consignment factories and make arrangements for production. The production status is also communicated to Japan every day.
As for quality control, when a problem occurs, I go to the site to see the actual product, check the current situation, and work with the person in charge at the partner factory to make improvements in order to reduce the amount of losses. The partner factory originally specializes in cotton, but most of Toyo's fabrics use polyester filament yarn. At first, it was difficult to produce with filament at the consignment factory, but after guidance from Toyo and others on how to do it, we were able to achieve success.